Port of Alaska Modernization Program

Port of Alaska Modernization Program
Navigating a Highly Dynamic Environment and Complex Permitting to Repair Dire Issues at Alaska’s Integral Port
The Port of Alaska is a key intermodal transport hub essential to freight movement in Alaska. It efficiently links marine, road, rail, pipeline and air cargo systems to connect communities, military bases and other destinations across the state. However, the Port’s condition is critical. Pipe piles have corroded and begun to split apart. Steel sleeves have been installed as pile jackets around corroded sections of piles to help maintain operational capacity, but these jackets have a limited benefit and they do not address seismic concerns. An earthquake in 2018 exacerbated existing damage as well.
If the damage is not addressed, the Port will have to continue reducing load capacities at the existing docks. And if port facilities fail before a replacement is available, the transportation challenges of moving these products become almost insurmountable, because there are no other facilities in Southcentral Alaska with similar capability or capacity. There is no reasonable alternative to modernizing the Port because it cannot be economically replaced elsewhere. In short, this project is vital to Alaska’s economy.
The Port serves deep-draft vessels that operate year-round to transport cargo faster, in cost efficient manner, and more reliable than any other means. It is Alaska’s only National Strategic Seaport and a critical piece of national defense infrastructure. The port is the primary entry point for fuel and cement in Alaska, upon which the transportation and construction sectors of the Alaska economy rely to maintain their business operations.
Jacobs and HDR have teamed together to provide program management for the five-phase modernization program, an approximate $1.5 billion program to replace nearly all of the existing port infrastructure. HDR’s role includes procurement, environmental services including all permitting, and construction administration services.
In 2022, construction is wrapping up on Phase 1, which is a new Petroleum and Cement Terminal to the south of the existing cargo docks.
Phase 2 consists of construction of two new cargo terminals as well as demolition of two existing cargo terminals, one of the old petroleum terminals, and reconstruction of the North Extension Stabilization 1 Project, which will stabilize a previously installed cargo handling and storage area. Construction of the cargo terminals are scheduled to begin in 2025-26.
Phases 3 through 5 include: replacing a second petroleum terminal; completing the North Extension Stabilization 2 Project and finally demolition of the third older terminal.
Funding has been gaining momentum — HDR prepared cost-benefit analysis that helped win two grants totaling $45 million for Phase 1.
Procurement With a Focus on Alternative Delivery
With a complex series of projects, each with their own unique challenges, there’s no one-size-fits-all delivery method.
Instead, our team has let contracts with a variety of alternative delivery methods. Just in the first two phases, the program has used four delivery models: construction manager/general contractor, progressive design-build, conventional design-bid-build and design-build.
Each procurement method was strategically selected to meet individual project circumstances.
A stabilization on the north extension had some safety complexities, and a progressive design-build contract allowed the owner to be more involved in the contract during the design phase and decision making. After a delay and reconfiguring of the contract, the contract is now moving forward as a design-build.
The replacement of the administration building is also using a design-build contracting method, and the new cargo terminals will be set up as design-bid-build contracts.
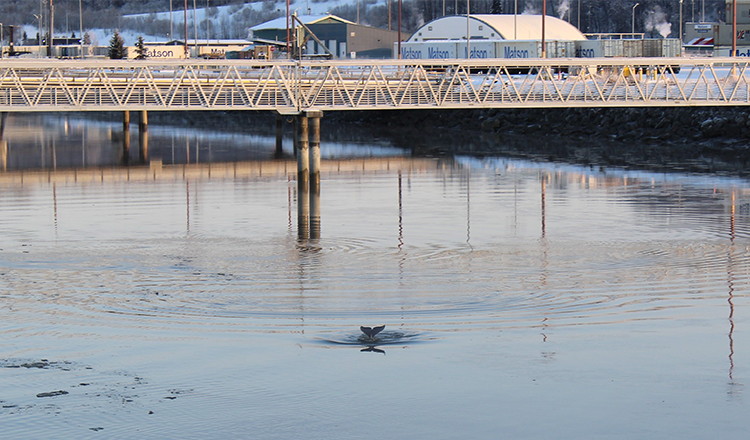
Building the Port While Protecting a Highly Endangered Whale
The port is located on the shores of Cook Inlet, the home of the Cook Inlet beluga whale, a highly endangered population and subspecies that is genetically distinct from beluga whales in other parts of the state. It is estimated that only about 279 individuals remain in this beleaguered population, and protecting the beluga whales from disturbance, especially elevated sound levels from pile driving operations, is critical to successfully constructing the new Port facilities. The permitting process for construction near these at-risk marine mammals is highly complex, and the project was required to implement major precautions to ensure that the work would not negatively impact the beluga whales and other marine mammals.
In the first year of construction, the port was authorized only 55 beluga whale “takes” (an incidental disturbance or harassment authorization issued by the National Marine Fisheries Service due to hydroacoustic impacts associated with pile driving). After 55 takes were realized, the project would be shut down for the construction season, creating a construction situation with a high risk for costly project delays.
The solution: Be proactively vigilant so that the work could be halted before the whales get too close. At all times during in-water pile driving, 11 marine mammal observers were spread across four monitoring stations to scan with high-powered binoculars, and if beluga whales were spotted, construction was halted.
This robust monitoring program was proven to be highly successful in avoiding potential disturbance to beluga whales and other marine mammals. In the first year, the project only used 30 takes of the 55 takes allotted, allowing construction of this critical facility to proceed. The marine mammal monitoring program has been successfully implemented for several construction seasons, and the Petroleum and Cement Terminal is now nearing complete, providing security to Alaskans as other phases of construction continue.
Overseeing Complex Construction Conditions
The HDR construction administration team worked 2020 installing 71 each (48”) diameter piles for the foundations and approaches to the new Petroleum and Cement Terminal and 2021 installing nine each (144”) diameter mooring and breasting dolphin piles. The 144” piles weighted between 255 tons and 311 tons each. These piles were installed in the fourth largest tidal conditions on earth, ranging 30’ +/- twice a day. These extreme tides affected how pile installation occurred, to include extreme currents generated by these tides and the elevation of the work barges relative to pile locations. The superstructure of the terminal was assembled by a series of precast concrete blocks, knitted together with massive cast-in-place concrete pours. Both the piling and the superstructure was supported by templates and falsework which needed to be constructed to support these permanent works.
The HDR team processed over 600 RFI’s for the two contracts on the Petroleum and Cement Terminal. All of these RFI’s required a full understanding of the questions asked, effort to make sure that the design intent was met and timely response to ensure the construction schedule wasn’t affected. Additionally, dozens of change orders needed to be scoped, price proposals reviewed, documented and executed.
In addition, the team worked around several complexities:
- In-water work could only occur during ice-free conditions — six and a half months per year. This meant working seven days per week, 12-plus hours per day to make schedule with only a handful of days off.
- The Port remained fully operational during construction including freight deliveries, fuel deliveries and ongoing dredging operations. The HDR team worked with Port operations staff, dredging contractors, and fuel delivery users to keep each operation moving, with minimal disruptions to the construction activities.
Federal government grant funding required the project use American products and materials. In a globalized material environment, this required much diligence from the construction team to ensure that materials and equipment were domestic sourced and just as important, had the proper documentation to verify these funding conditions.
