
Experts Talk: Optimizing the Airport Construction Safety and Phasing Plan Process, with Joe Grubbs
Experts Talk is an interview series with technical leaders from across our transportation program.
Strong Project Coordination Uncovers Efficiencies, Lessens Disruptions
The construction safety and phasing plan process is federally mandated for all airfield projects and can be a complex tangle for airports uneasy about looming changes to normal operations. But when done well, it can be an opportunity to get stakeholders on board early and uncover efficiencies that can lessen those disruptions. The resulting plan can help guide airports smoothly from project groundbreaking to ribbon cutting. In this interview, our Aviation Technical Director Joe Grubbs, P.E., shares ways to make the CSPP process as efficient and useful as possible.
Grubbs has nearly three decades of experience in the aviation industry, with expertise in a broad range of complex airfield design and construction projects. He is working on our projects to modernize the Pittsburgh International Airport facilities, to rehabilitate the commercial runway at Blue Grass Airport in Lexington, Kentucky, and to design a new runway and taxiways at Tucson International Airport.
Optimizing the CSPP
Q. What are the pain points of airports in developing a CSPP?
A. Airports operate systematically. So any time you introduce something that is out of the normal routine it invites an element of risk. We are all creatures of habit and an airfield's flow is also based on habits — a taxi pattern may have been used for years and everybody involved expects the pattern to stay the same for years to come. When that taxiway is impacted by construction, it disrupts the routine and that introduces an element of risk.
Besides risk, some stakeholders can feel left out or unheard if decisions are made from the top down without input. HDR often acts as a subject matter expert for clients in the federally-mandated Safety Risk Management process that the CSPP typically triggers, as was the case in a recent SRM panel for the Philadelphia International Airport. An important part of that process is fully defining the project through the construction phase, including sharing the phasing plan with all the airport stakeholders such as airlines, airport vendors, governing authorities, emergency responders, general aviation representatives and more. We take input from the stakeholders to get their constraints, work with them on their needs and help develop a plan that all can agree on while prioritizing safety and completing the work as efficiently as possible.
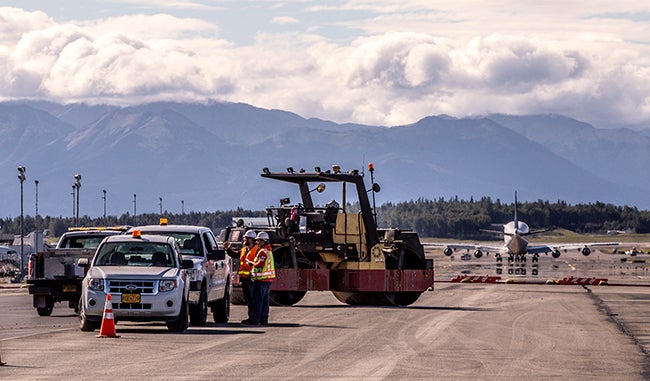
Q. Why is it important to engage all parties early in the construction phasing process?
A. We have a distinctive process of early engagement that we recommend to all our clients, so that all the major stakeholders can see the process of how the construction phasing and maintenance of traffic plan is developed. When they see the process, they're more likely to buy in and more likely to be an active, helpful participant. This also means that stakeholders can bring issues forward and identify impacts that a design team may not necessarily understand initially.
It’s also helpful for many of those involved to know a ballpark timeframe for when the construction is going to take place. For instance, airlines need to know six to eight months in advance of when a taxiway or runway is going to be out of service because that's how far in advance they do their schedules.
Q. What does a typical engagement approach look like during CSPP development?
A. Once we know what the project is, then we can start breaking it up into pieces in order to have structure. Right after the 30% design level, I like to get with our clients and have them consider engaging those who will be affected to define the project to them so they know what the project is all about and why it’s needed.
Then we start talking with them about what kind of constraints we are looking at. For example, maybe the aircraft rescue and firefighting unit at the airport needs to keep a specific pathway clear at all times in order to respond quickly in an emergency. Or perhaps a specific gate needs to be available at specific times because it’s the only gate that fits an airplane. A Boeing 787, for instance, requires certain features that may not be at every airport gate. Specific air traffic demands must be addressed and mitigated, including the possibility of airlines temporarily swapping out replacement aircraft. Identification of these key constraints are a critical part of our work.
We start getting all of those ingredients into the recipe. And once we get that information then we go back and begin our analysis. Our goal is to see what we can do to make this project move forward while keeping the airport environment as near its normal operations as possible. Sometimes you can accommodate that, sometimes you can't.
We develop a number of construction phasing alternatives for the client to consider and we vet those possibilities with the client. Then, with their approval, we move those forward to the larger stakeholder group, keeping them informed.
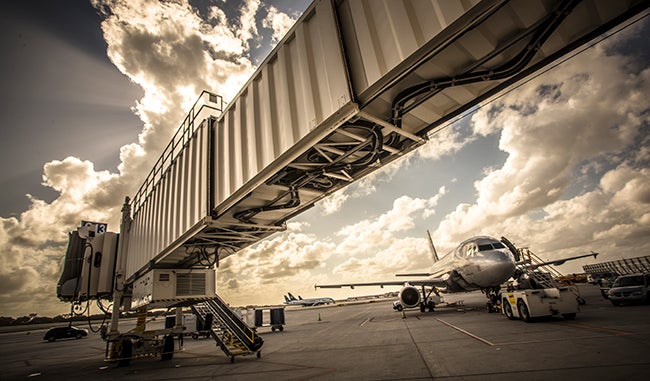
Q. Explain the importance of encouraging flexibility among stakeholders and exploring more options.
A. On almost any airfield project, there are a number of different stakeholders that have a variety of different operational needs. All of them want to minimize the disruption to what they have to do. Our job is to meet those desires as much as possible, while prioritizing safety, budgets and efficiency during construction.
To that end, we work with affected parties to see where changes can be made to the CSPP that won’t unduly affect them but will benefit the project. Perhaps an airline had asked that a section of the airport be kept open until at least 10 p.m. every night to accommodate a late flight. But in talking with the airline more, it may turn out the area only needs to stay open that late five days a week. The other two days, it can be closed at 2 p.m. and construction crews can start their work eight hours earlier.
That extra time can be key. A four-hour work window is extremely expensive as opposed to an eight-hour work window. Even better is a nine-hour work window because it takes the first half-hour and the last half-hour to put up construction safety devices and to take the construction safety devices away. That leaves a solid eight hours of production for contractors and that's when our clients get their best construction prices.
Similarly, if we can make the work area a little larger and not impact operations too significantly, it pays dividends on the backside in the form of lower prices. Maybe we can close one extra gate, or temporarily relocate operations to provide extra square footage for construction. Each part of the plan is examined to find those opportunities for higher efficiency.
That’s important because today’s funding realities mean every dollar is really spoken for. By looking for places to expand work areas or times, we can help secure better unit prices for our customers. Then they can stretch that dollar and do as much as they possibly can on the airfield as they make that investment in either rehabbing their existing pavements or building a new site. Maximizing that investment while doing it safely on an airfield has always been my passion.
Q. After the CSPP plan is drafted, how can its approval and implementation be streamlined?
A. As design nears completion, we narrow the phasing scenarios down to the best option, based on the conversations we’ve had with stakeholders and our client. That plan then goes to an SRM panel or an SRM workshop, depending on the process and terminology of the particular airport.
What we like to do is to make sure that the airport, the relevant FAA airports district office and the FAA air traffic organization are in the same SRM process. In the past, there have been times when FAA air traffic completes one SRM and the district office holds its own SRM.
We've been successful in getting those combined into one process, which is more efficient for clients. I implemented this strategy as a program manager at Philadelphia International Airport, for instance. As SRM participants go through the plan and assign risk levels and mitigation strategies, it encourages agreement from the beginning. Combining the panels ensures everybody is on the same page on the project and that they're converging instead of diverging. That saves us time on the backside, instead of having to coordinate and mediate between two SRM panels.
With that SRM process complete, it allows us to finish the CSPP and finalize the construction phasing plans for the contractor, and then get the job bid and the project realized.
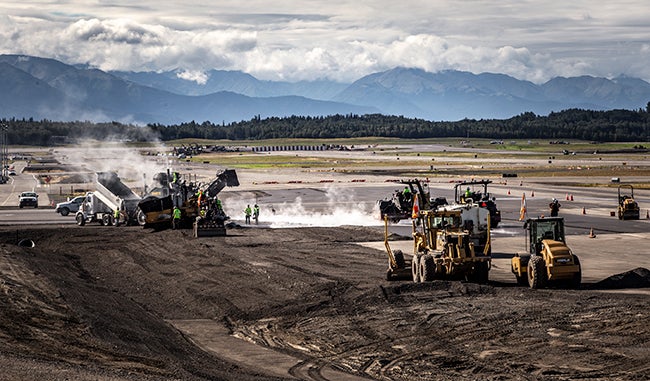
Inspiration and Advice: Joe Grubbs
Q. How did you become a subject matter expert in the realm of SRM and CSPP?
A. Construction has always been a passion of mine. When I started my career, I was a contractor, then became a construction manager in the aviation field. In the early days, I would do construction scheduling and construction phasing because I had a fairly good understanding of the equipment and the productivity. Starting out as an estimator for a contractor, I understood the process of how contractors price performance and price risk. So it became a natural fit to start advising clients on the process, letting them know when something can’t be constructed a certain way or there was a better way to do it.
I started seeing how some of the phasing was really costing our customers money, just because the areas weren't large enough for contractors to be productive. There's a time and place for that if you're working on a critical piece of infrastructure and you only have a small window and small area. But I wanted to help our clients to stretch the areas that we give the contractors so they can get better prices but do it in a safe manner to maintain as normal airfield operations as possible. I went down that path many, many years ago and continue to do it to this day.
Q. What advice would you give to engineers just starting to work on aviation design projects?
A. First and foremost, read and understand the FAA’s 150 series of Advisory Circulars. The criteria contained in these documents are the basis for almost every commercial and general aviation airfield design in the U.S.
Secondly, once one builds a solid foundation in understanding the Advisory Circulars, apply that understanding to get broad airfield experience and work toward becoming an expert in one particular component of airfield design that peaks your interest, be it pavements, drainage, electrical, or CSPP’s.
Lastly, recognize that every airfield operates differently depending on the volume of air traffic and in various weather conditions. Get to know and understand how the airfield operates because the project that you’re designing will likely disrupt the normal aircraft traffic ingress and egress flow/routes. Therefore, it’s important to get to know the professional men and women with airfield operations, FAA air traffic control tower and the air traffic managers of the airfield users. These folks are responsible for moving aircraft around the airfield in a safe and efficient manner. Understanding their viewpoint, along with the local construction capabilities, and designing accordingly many times directly influences the overall success of a project.
Each Experts Talk interview illuminates a different aspect of transportation infrastructure planning, design and delivery. Check back regularly for new insights from the specialized experts and thought leaders behind our award-winning, full service consulting practice.