
Experts Talk: Bridge Asset Management Through Rope Access Inspections with Erin O’Malley
Experts Talk is an interview series with technical leaders from across our transportation program.
Up-Close Inspections Provide Flexibility and Fill a Critical Role in Maintaining Bridges

Keeping bridges in good condition starts with understanding their existing weaknesses and spotting any concerns long before they become problems. Regular inspections provide this insight, and performing them is vital for effective asset management of bridge inventory. For some bridges, however, conventional inspection access methods aren’t practical or possible. In such situations, rope access inspections provide the solution.
Erin O’Malley, P.E., is our industrial rope access leader for bridges and structures, coordinating a national team of inspectors that work on some of the most iconic bridges in the U.S. Among the hundreds of structures she has inspected are the Bayonne Bridge in New York/New Jersey, the Marc Basnight Bridge in North Carolina, the Shenandoah River Crossing in West Virginia, and the Golden Gate Bridge in San Francisco. In this interview, she explains why bridge owners turn to rope access inspections, why the special skill is still needed in an era of new technology such as drones and how the practice is changing bridge design.
Q. What is rope access inspection and when does it make sense over other bridge inspection access methods?
A. Rope access inspections are most often used where access is difficult and conventional access methods either are not possible or have some other drawbacks. In general, this means remote bridges, small or old bridges with weight limits, very large bridges with height or reach access difficulties and when clients want to minimize lane shutdowns.
Conventional methods of accessing bridge elements include ladders, bucket trucks, boom lifts, and under-bridge inspection trucks (or UBITs), but all of these methods have limitations. Sometimes you can't physically get a piece of equipment on site. Ladders, bucket trucks and boom lifts can only reach so high, and UBITs can only reach so low. Ladders and lifts are only useful when the ground below the bridge is traversable, and UBITs require lane closures to operate on the bridge deck.
In these situations, rope access provides an alternative solution. Industrial rope access inspectors use ropes and climbing gear to get close to a bridge and work while suspended in a harness. Inspectors can climb up and down, move diagonally across multiple sets of ropes or traverse horizontally along I-beams or tensioned ropes.
Other times, conventional access methods work, but it might make sense to use rope access because it is less invasive. You can usually get on a bridge without closing a lane or interrupting traffic or pedestrian movement. And a lot of times people don’t even notice that you're there.
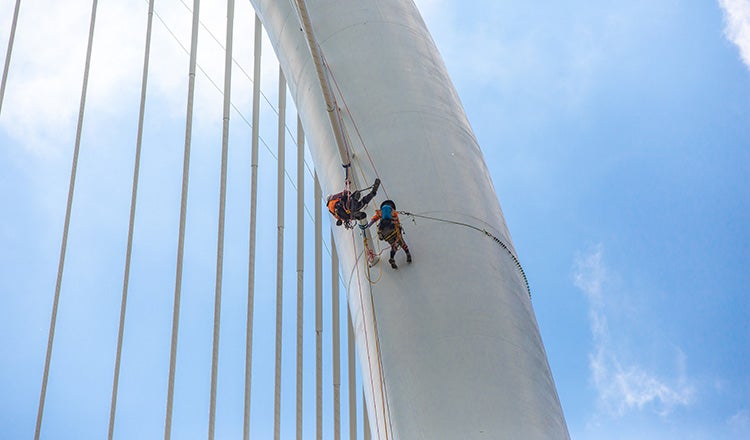
Q. In an age of increasing technology, including drones with high-quality cameras, why are in-person rope inspections still needed?
A. Drones only replace inspectors’ eyes, not inspectors’ hands. That’s important for fracture-critical bridges in particular. The federal requirement for a fracture-critical inspection is to be hands-on, and that means you have to be able to touch the bridge. Inspectors must be able to chip the concrete, scratch the paint, and wiggle the bolts. They need to be able to do nondestructive testing. Sometimes you'll have a really corroded area and you just see a little pinhole, but then you start banging with your hammer and that opens up a pretty substantial hole. With a drone, you would never know how big that hole actually is. That's why we haven't been replaced yet.
However, drones can be effective at identifying problem spots in conjunction with rope access inspections. Drones are flown either ahead of time or concurrently and used to inform inspectors of places to focus their attention. Sometimes they’re also used for documentation so that if something comes up later and there’s a question about a specific section, inspectors can go back and review video footage.
Q. You’re also a bridge designer. How has your inspection work impacted your bridge designs?
A. I think that being a designer makes you a better inspector. And being an inspector makes you a better designer. I've definitely seen some bridges with access holes that are only a foot wide or a few feet tall and thought, "Yeah, I’m not going to fit through that." Or the beams are really close together to the point where you can't get your head in between to inspect them. Being in the field gives you a sense of scale. If you only design things on paper, sometimes you may not realize how tiny or big things are. But if you've gone out into the real world and seen a bearing or a bolted field splice or any element that is represented with just a line on the plans, you see how much space it actually takes up, and you definitely design things differently.
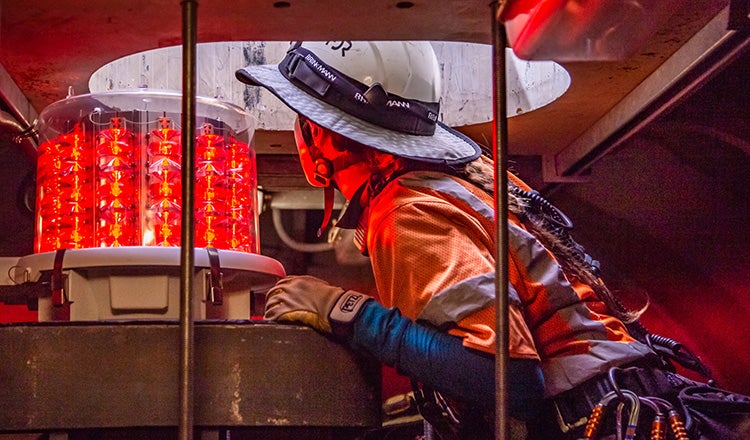
Access for maintenance and inspection should always be a priority. Designers can sometimes put things way too close together so an inspector can't see all the pieces, or alternatively space them out too far. They might put a catwalk on their bridge, but it's all the way to the left. That's great, but how am I supposed to see the right side? My No. 1 piece of advice to designers is go out in the field. Even if they never do it again, I think just one field experience will help inform their design work.
Being out in the field also shows the importance of design improvements made over the decades. For example, if you have a bridge and it's sloping a little bit, any water is going to run along that bridge to one end. The bearings at the downhill end are going to be much more corroded. Now, we add a waterstop, a bar on the bottom of the bridge that catches water and directs it off the bridge. But on older bridges they didn’t do that, and when you get out there and you see older bridges that don't have a waterstop, you see how corroded the bearings are. Back in the office, when designing a new bridge, I better understand how important that tiny nonstructural element is.
You can also see what realistic maintenance is when you do inspection work. You get to see where problems are more likely to come up and then you can design around that. When you're a young engineer designing a bridge joint, you might assume that the owner is going to go out there and clean this joint every six months, so the size of your joint opening will never be compromised. But then you go out into the field, and you see joints that haven't been cleaned in years. They are full of dirt or grass, and the joint no longer functions as the designer intended. You realize that ideal scheduled maintenance and actual maintenance performed are not the same thing. You can deal with that by having a better design that doesn't need to be maintained quite as often or is easier to maintain. And by designing a bridge that is easier to maintain, it makes the owner’s job easier as well.
Q. How have rope access inspections changed bridge design?
A. I see design changing in two ways, and it largely depends on the priorities of the project.
First, clients are thinking more about inspection during the design phase to control future maintenance costs. Inspection requirements developed over the last 50 years have created a larger need for access. Bridges built decades ago weren’t necessarily designed with hands-on or detailed inspections in mind. That can make them more difficult and costly to inspect today. Rope access may be the only option for many of these, and rope access can be more expensive than conventional options in some cases. As new bridges are built, owners are ensuring they’re designed with access for future inspections knowing that they will have to pay for these over the life of the bridge.
Second, as clients realize that rope access inspection is an option, they understand they can plan for it, and as a result they can design large signature bridges differently. This has big implications for structures where aesthetics are a high priority. Instead of covering a bridge in catwalks, designers can decide upfront that they’ll inspect via rope access down the road. This allows more options when designing a new bridge — higher towers, fewer access holes, etc. The alternative is usually something that's not as aesthetically pleasing, often involving permanently attaching something to the bridge. With rope access, however, a team can go out there, do its inspection and then leave for two years. It makes it very attractive from an aesthetic point of view. With rope access in their pocket, designers and owners can know they’ll still be able to reach every nook and cranny, but still preserve the look they want.
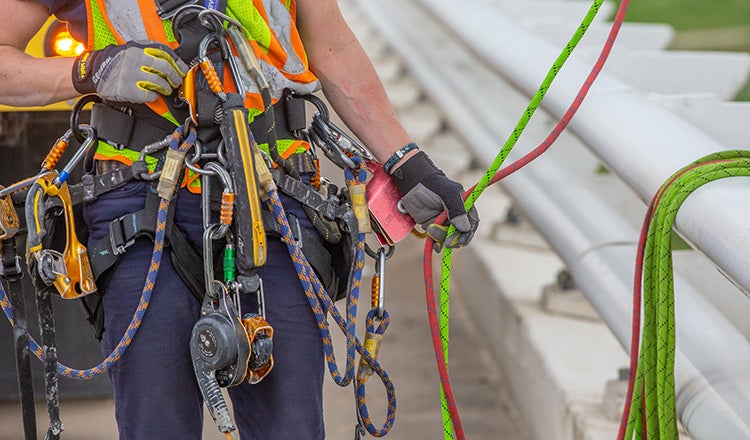
Q. What added safety and experience considerations are there for a rope access inspection team?
A. Each member of our team is certified by the Society of Professional Rope Access Technicians, or SPRAT. We have more than two dozen SPRAT Level 1 inspectors with experience across North America. They’re led by multiple SPRAT Level 2 lead technicians and SPRAT Level 3 supervisors who can provide both rigging and inspection services. Each inspector must be recertified every three years, with the same rigour of testing as their original certification.
Within HDR, we also conduct annual safety training. All our rope access inspectors come to a training facility for two days, at a minimum, every year, where we practice rope access skills and rescues. We have strict requirements for refresher training to ensure that everybody is well practiced and our team members know how to work safely.
Performing our work safely is of the highest priority. Every rope access job starts with safety and access plans created by the SPRAT Level 3 team leader after studying the as-built documents and previous reports. And each day on site, the team starts with a discussion about safety, including anticipated hazards and rescue plans.
The result is that we are prepared for almost any situation, whether wind is blowing, rain is falling or a big wasp nest is waiting under a bridge. A culture of safety, a team we can rely on and extensive preparation help us to tackle whatever occurs.
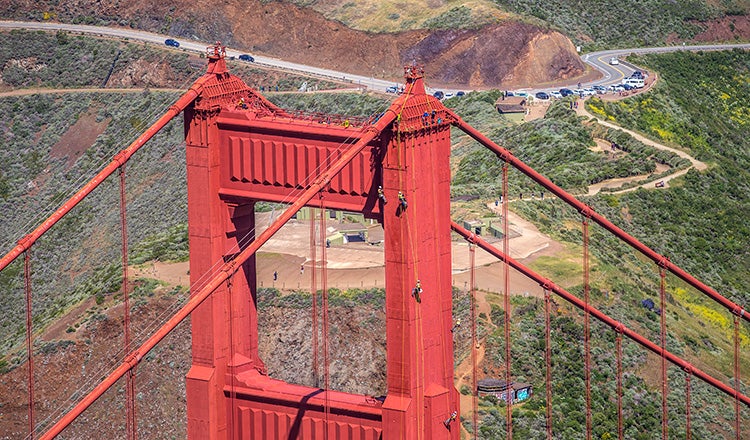
Inspiration & Advice
Q. How did your career lead you to rope access inspections?
A. I started out as a bridge designer, which I think is how most people do it. I'd been working for HDR for about a year in Texas as an engineer-in-training straight out of graduate school. When a local project leader asked me if I was interested in going out in the field, I said yes, not really knowing what I was getting into. So I went to Houston, did some routine inspection work and thought it was interesting. Then they kept calling me back to help. I became a regular part of the Texas inspection team, and after a couple of years and getting my P.E., I became an inspection team leader. After a couple of more years, I was asked if I was interested in adding a rope access certification, and that led me to the rope access group. From there, I just kept gaining experience, both in Texas and nationally, and worked my way up. Now I’ve worked all over the United States, to the point that if you showed me a photo of a random bridge, I could make a pretty good guess as to which state it’s from.
Q. What advice do you have for somebody interested in a similar career?
A. Be open to opportunities even if they are different from your general career plan. When I was in college, I did not want a field job. I pictured myself in an office with a career focused primarily on new design projects, and when I started with HDR, that was the path I was on. I didn’t even know that bridge engineers could also be bridge inspectors.
Don’t be afraid to take it slow. I see young engineers coming out of school who want to jump straight to project management or to only work on the high-profile jobs. But if you take the time to learn the foundational elements of your discipline, you’ll be a better team member now and you’ll be a better leader in the future.
Each Experts Talk interview illuminates a different aspect of transportation infrastructure planning, design and delivery. Check back regularly for new insights from the specialized experts and thought leaders behind our award-winning, full service consulting practice.