
Experts Talk: Intermodal Freight Terminal Optimization with Chad Hewitt
Experts Talk is an interview series with technical leaders from across our transportation program.
Designing Sustainable, Flexible, Efficient Links in the Global Supply Chain

Intermodal rail terminals are a critical link in the supply chain, helping direct freight, store it and ultimately get it to its final destination most efficiently. As the global logistics network continues to deal with disruptions of the pandemic, the optimization of these key facilities will help keep goods moving, improve the resiliency of operations and reduce future slowdowns and interruptions.
Chad Hewitt, P.E., has managed the design and construction of intermodal facilities and gate systems across North America, serving nearly all major railroads and several ports over the past two decades. In this interview, he explores how intermodal yards can improve the efficiency of existing yards, addresses trends in sustainability and offers examples of how facilities can create new options for supply chain flexibility.
Q. How can intermodal yards make better use of their existing space to improve operations?
A. Railroads and ports don’t have a lot of available space to expand anymore, particularly at their urban and coastal locations. Instead, they're going to have to eke out every percentage growth opportunity they can within an existing footprint. So the natural approach is to stack inventory. Freight is typically moved and stored in containers that are essentially giant boxes, which are readily stacked. The complication is that though physically easy, it can require a new level of management and planning. Yards need to understand how to retrieve the container they want when they want it, even if it’s in a stack five tall and five deep. That requires a new mindset and a new operating approach.
Yards will need to implement newer crane styles that can stretch out over containers and selectively dig into a pile. Side handling equipment — basically large forklifts — can be less costly on a per unit basis, but they don’t provide this selectivity and require moving every container on top of and in front of the one needed. For example, if there’s a pile of containers five deep and five high, and one in the back at the bottom is needed, a container handler will need to move 24 boxes to get the right one. An overhead crane, on the other hand, would need to reach down and move four containers.
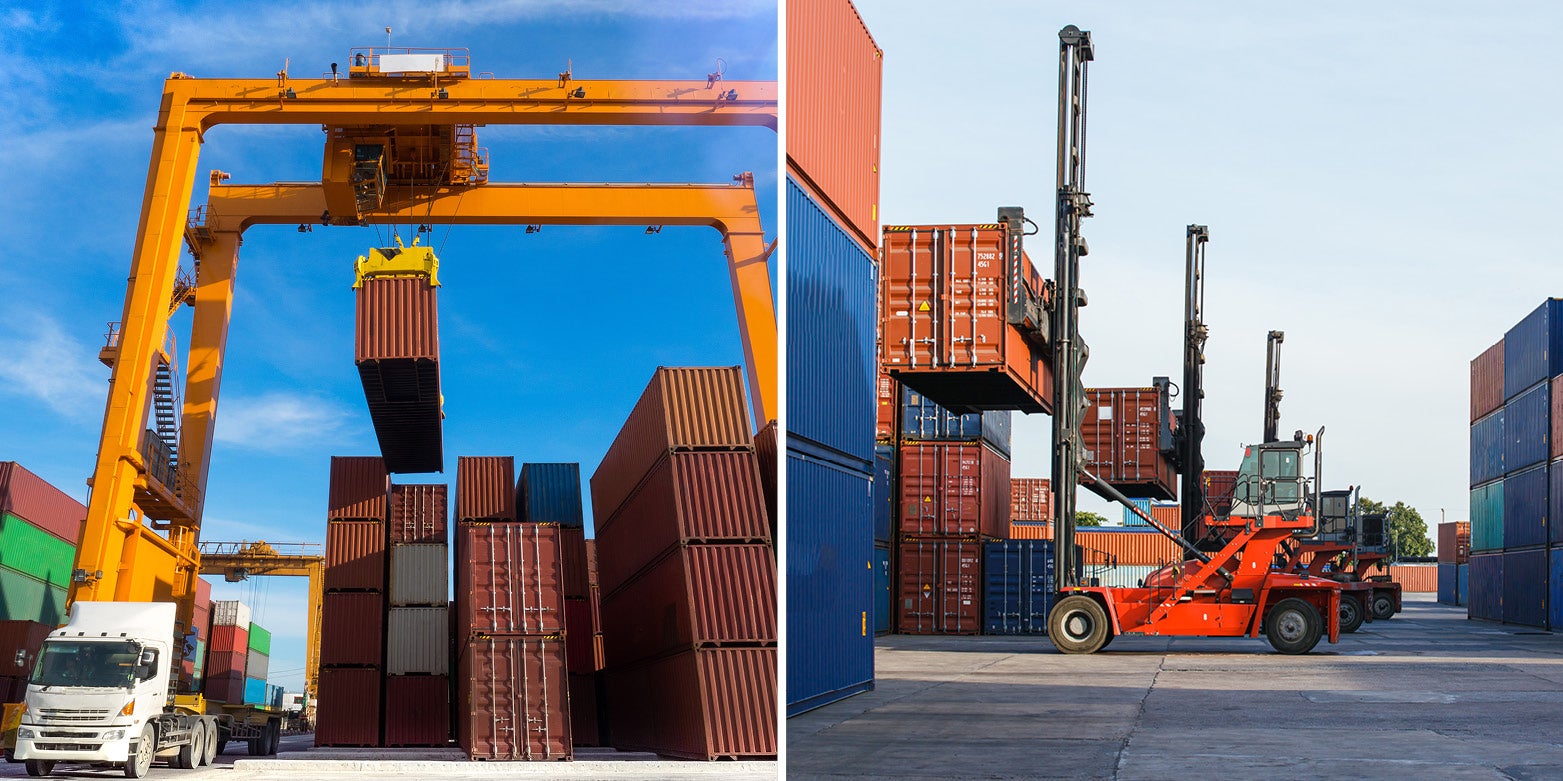
That increased efficiency in turn requires a different facility design to support the equipment. It may have longer rows of stacked containers instead of parking for trucks. Craneways are added to support larger cranes and their heavier loads. There’s a mechanical aspect, there’s a civil design aspect, there’s technology, and an operating plan; it’s all intertwined and it’s therefore necessary to consider all of these facets when redesigning a facility or designing a new one. This approach, however, is not new to the industry, having been employed at intermodal yards outside of the U.S. and at ports.
Q. What are the key components of designing a major redevelopment or a greenfield intermodal yard that will be adaptable long-term?
A. It’s important to bring in a team that understands both the civil design requirements of a yard as well as intelligence, automation and even Internet of Things or IoT. Program managers or lead designers who understand those aspects will help produce a terminal or yard that’s conducive to implementing these systems in the coming years and bridging the divide between operations and design.
Understanding these new advancements in the industry can have significant implications on site development and design. It could be very impactful, affecting what crane to use and how to use it, whether you're going to mount everything on chassis, or if you're going to use one big crane or two smaller cranes.
One of the biggest challenges, particularly in greenfield, is accurately capturing the market segment the yard will be serving. Will it handle fast-moving freight or slow-moving freight? Will it be a mix of international and domestic freight, which have different container sizes? Will the loads be heavy grain or lighter products? Knowing the answers to questions such as these will help right size the facility from the get-go. Even if the facility changes its focus down the road, the right equipment design can help reduce the impact of these changes.
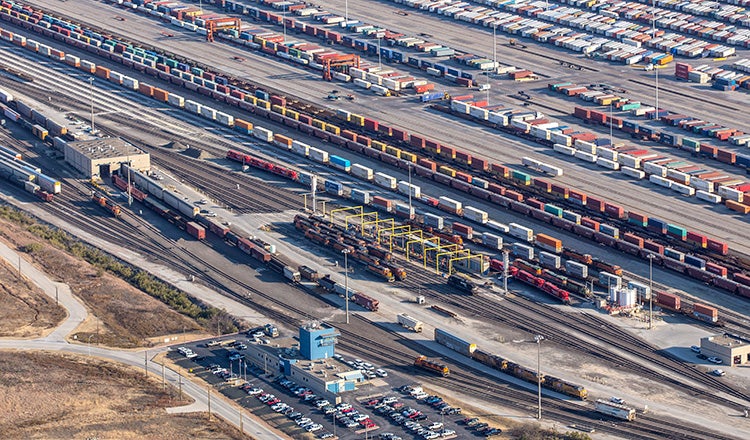
Q. How are intermodal yards and terminals adapting to reflect new environmental and sustainability considerations?
A. Intermodal freight movement has long been one of the most environmentally friendly ways to move goods. Next to water, rail is the most efficient way to move a ton of goods. Within yards themselves, though, there are new techniques to increase sustainability.
There's a push towards electrifying equipment rather than using diesel engines. Instead of 10 cranes each with its own diesel engine, the cranes may be put on one conductor bar that is electrified. Electrified cranes also allow for easy recapture of energy during deceleration or downward hoisting moves. This recaptured energy can be stored on the crane or shared with the greater pool of cranes operating within a terminal, not only avoiding wasted energy, but also offsetting peak electrical loads. Reduction of peak loads reduces the cost of purchasing the electricity for the terminal and makes it possible to rationalize the electrical distribution infrastructure required within the site.
Many terminals are also testing electric horizontal transport, the vehicles that move containers on wheels around the terminal. That is becoming increasingly attractive as battery technology advances. However, intermodal yards going that route need to address it in the design phase, because there are sizable infrastructure considerations to charging a large fleet of equipment quickly.
Advancements in lighting have also taken place in recent years. LEDs have long been used inside buildings, but there’s also been significant improvements outside in making LED lights work on a large scale. The key is to focus on ensuring the light is targeted toward shining where it needs to be, rather than just throwing light down from a 100-foot tower. That way there’s not a lot of light pollution, which can adversely affect adjacent properties. That's a clear environmental improvement over past installations. Smart lighting that comes on only when needed is also possible within a stacked terminal, placing lights upon the cranes that focus on the immediate area of work rather than blanketing the entire site continuously. Automation of the lift equipment also impacts the lighting design as automated equipment requires less light than a human operator would.
Q. What disruptors and trends can the intermodal industry expect in the next few years?
A. Challenges of capacity and throughput are likely to remain for the foreseeable future, as will labor shortages. And partly as a result of those continued shortages in labor, we will see increasing interest in automation. Anything that can be done to automate and reduce the need for full-time human involvement is going to be of great interest. Achieving full automation is often very difficult, but I expect to see more movement toward human-assisted automation, so to speak. If we can have a machine do a job on its own 85% of the time, with a human involved the 15% of the time when the job is more complicated, that’s a big difference. Then one person can oversee three or four cranes, instead of needing one person per crane. And that person may be able to do their job remotely, in a more comfortable office instead of climbing up into an actual crane. At smaller terminals, that could allow that one person to handle multiple tasks or functions intermittently.
There's also a lot of opportunity to make things efficient through operating intelligence and working closer with customers and partners. Improved communication will lead to improved efficiency. It's as simple as the railroad or port knowing when a trucker is going to come pick up a specific container. It could be very strict, a narrow window of an hour or less. Or it could be sometime within half a day. This improved communication can give the operator of the terminal insight on when they need to touch a box or dig it out. With accurate operating intelligence, idle waiting time for trucks could be dramatically reduced and yards themselves could be much more efficient in moving containers.
And I expect new intermodal yards and terminals to continue to be built farther from urban centers. BNSF’s Logistics Park Kansas City, developed over the last decade, is a good example. It’s located about 35 miles southwest of Kansas City, and a lot of the businesses that support that facility have moved outside the city as well. Now you can't even call it a bedroom community because workers are living out there near this logistics park that handles freight transportation as well as the warehousing all in one. I think we’re going to see more development like that.
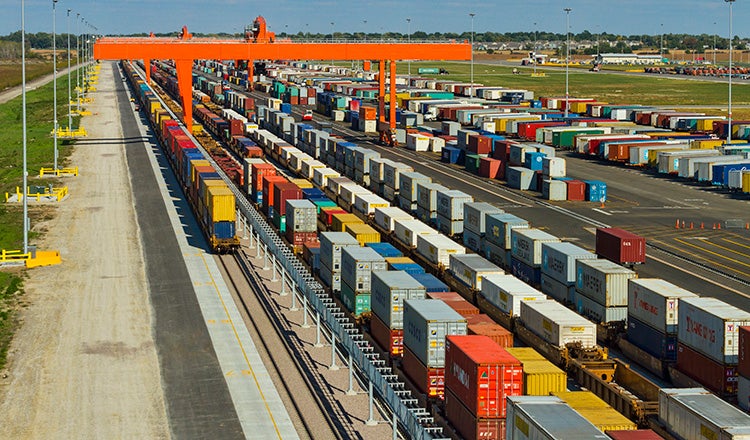
Q. How can railroads and ports use intermodal yards to build in the flexibility they need to meet daily demands as well as unexpected peaks or dropoffs?
A. The biggest consideration is efficiently getting material off the dock so it doesn't sit there and lead to more congestion. A remote sorting facility can provide help with that task. Instead of sorting containers at the dock, all but the highest priority could be put immediately on the next available train, taken to a facility farther inland where space is more available and sorted for their destination. Getting them off the dock as quick as possible onto a rail car and then sorting them later could offer some tremendous economies of scale.
We could also see facilities being built that are little more than a remote warehouse. Say there are imported materials coming in from a vessel. They’re not needed at the factory for a month so they’re sent to a facility in the middle of the desert and sit there in a container rather than on prime real estate in the city. Then, a few days before the materials are needed, they’re put on a train and delivered to the factory just in time. We’ll see more solutions like that which take advantage of cheaper real estate and free up more expensive space for the highest priority freight, providing some elasticity to the just-in-time logistical network that has recently shown to be susceptible to disruption.
The experience of the Georgia Ports Authority in 2021 offers a good example of a flexible solution that can be replicated by others. With container dwell times and ship backlogs increasing to record levels at the Port of Savannah, the GPA used inland container pop-up yards to rapidly cut congestion and keep freight moving. HDR helped implement and find funding for the expansion of a series of facilities served by trains and trucks, dramatically cutting the volume of stored containers at the port. From the program’s beginning in late November 2021 to mid-February 2022, the average dwell time for containers at the port dropped from 17 days to less than 10, with much of the difference attributed to the creation of these new inland facilities.
Inspiration & Advice
Q. How did your engineering career lead you to a specialization in intermodal rail projects?
A. My family has always been involved in railroading, so I knew about the industry growing up. Early in my engineering career, I had the opportunity to work on a large project for BNSF in Chicago, and I got to see the entire construction of an intermodal facility from start to finish. I found it really interesting. I was fortunate to have some great mentoring relationships on the terminal operations side, which was unique, but really helped provide an understanding of how and why things were done within the terminals. I discovered that everybody involved in these projects appreciated having an engineer who could speak to civil design while also understanding the operating specifics, which led me to where I am today.
Q. What would you tell engineers earlier in their career who are interested in intermodal facility design?
A. Take the chance to be part of an intermodal project and it will improve your understanding of a wide swath of disciplines. There's a world of opportunity in this industry and so many different aspects of engineering involved. You've got hundreds of acres of land with all kinds of paving as well as railroad tracks and large machines. There's every manner of utility involved. There's buildings, structures, lighting, telecommunications and more. It requires just about every aspect of civil and electrical engineering and maybe even a little mechanical engineering as well. You’ll always have something new to do.
Each Experts Talk interview illuminates a different aspect of transportation infrastructure planning, design and delivery. Check back regularly to discover new insights from the specialized experts and thought leaders behind our award-winning, full service consulting practice.