
CMAR in Aviation – Strategies for Success
How Airports Can Get the Most Benefit From Construction Manager At-Risk
The construction manager at-risk delivery method continues to grow in popularity on large, complex airport projects. Its collaborative approach and potential for schedule and cost-certainty benefits have made it a popular choice at major airports throughout the country and world.
At HDR, we have been a part of multiple CMAR projects at airports, including three terminal expansions at Fort Lauderdale-Hollywood International Airport, a runway replacement at Tucson International Airport and a new terminal at John Glenn Columbus International Airport. Drawing on this experience, some key strategies have become clear as ways to get the most benefit from this project delivery method: Engage early, prioritize collaboration, and have a deep understanding of roles and responsibilities.
First, some context. Under the CMAR method, the owner has a contract with a designer to design the project and a separate concurrent contract with a construction manager at-risk, or CMAR, to construct the project. The designer and CMAR are contractually required to work together during the design phase to complete the design and to establish a price for construction guaranteed by the contractor. CMAR, also known as CMGC, is one of the best delivery methods to identify, allocate and mitigate risk before the final cost of the project is determined.

Advantages of the CMAR approach include the ability for the owner to remain involved and strong collaboration between contractor and designer, increasing the probability of positive project outcomes for all parties, including other stakeholders. Challenges include navigating multiple contracts and not knowing a guaranteed construction price until later in the process.
At airports, the method can be particularly useful because projects often have limited construction windows. Runways may only be able to be shut down for a few hours at night, for instance. Having contractor input throughout the design process means all parties are aligned when it comes to what’s possible and the best approach for delivering a complex project. A contractor may point out that adding an extra hour to a construction window would be a significant savings or suggest alternative access options to maximize the usefulness of a construction window. That back and forth collaboration between parties during the development and delivery phases is a key feature of the method and an important part of the following recommendations.
Engage a CMAR Early to Avoid Rework & Lost Opportunity
In the planning and early design phase, it’s important that the owner initiates some design to provide a framework for the project, but there’s also a danger of doing too much before selecting a CMAR firm. Extensive design work completed ahead of the CMAR selection may need to be reconsidered after a contractor provides their feedback. By maintaining flexibility in the design, it allows the contractor to provide beneficial input on constructability and opens the door for value engineering opportunities.
Research published in 2020 on the use of CMAR at airports noted this issue, saying “it was key to select the CMAR firm early in the design phase so that the CMAR firm’s construction expertise can be used during the design process.” The research highlighted a project where a CMAR firm was not selected until the design was 60% complete. The result was less opportunity to engage the contractor for early management of design risks, and the owner subsequently changed its process for future projects to engage a CMAR much earlier.
To achieve the most benefit from the collaboration in a CMAR, it’s important to adjust expectations on the level of design. The 30% level of design in a CMAR project often looks different than a 30% level of design in a traditional design-bid-build project. Before the contractor is brought on board, items like schedule and packaging should be held less firmly. After the whole team is assembled, collaboration can lead to a better understanding of what design elements are needed first, what the critical path elements are and the packaging and phasing that is most efficient for all parties to achieve schedule and budget goals.
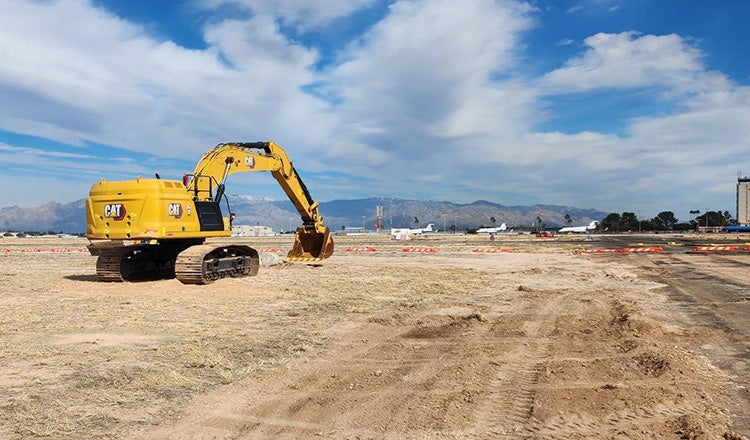
Prioritize Collaboration to Expedite Decisions
Realizing the benefits of the CMAR approach requires a designer and contractor who work well together and can collaborate to find efficiencies. Technical proficiency is important as always, but in a CMAR, it is also important to have leaders and a team that are open-minded, flexible and amenable to working together. Good communication, respect and the free flow of ideas that follows are what lead to innovation, efficiency and the true benefits of the CMAR approach.
Strong collaboration showed its value on a terminal project at Fort Lauderdale-Hollywood International Airport. As the lead civil designer, we understood that many of the aspects of our design would be on the critical path. By collaborating early (before 30% design) with the CMAR to understand items critical to their construction sequencing, we were able to better define early work packages and develop an expedited permitting approach for these key packages.
The development of maintenance of traffic plans can be a particularly beneficial focus at airports. Working through the design and construction process together identifies places to improve schedule and find opportunities for improvement. These plans impact how the team designs critical elements such as utility relocations, installation of required foundations and more on both airside and landside construction sequencing.
This collaboration also shows advantages in advancing critical schedule items through permitting. Building code officials and fire marshals can have a higher confidence when they see the owners, designers and contractors all coordinating and collaborating — working towards a common goal. Collaboration improves cost estimating with the ability to have designers and contractors validate each other’s estimates. And it allows for better informed decisions when contemplating changes to a project, with all parties working together to determine if proposed changes are feasible.
Weekly coordination meetings and key breakout sessions on critical design elements can help make important decisions as a team and gain early schedule advantages. In these meetings it’s important to have all the parties represented — CMAR, designer, owner and any authorities needed for permitting. A co-located office further aids in communication and can provide a setting for these regular team meetings as well as more efficient communication and coordination of day-to-day issues.
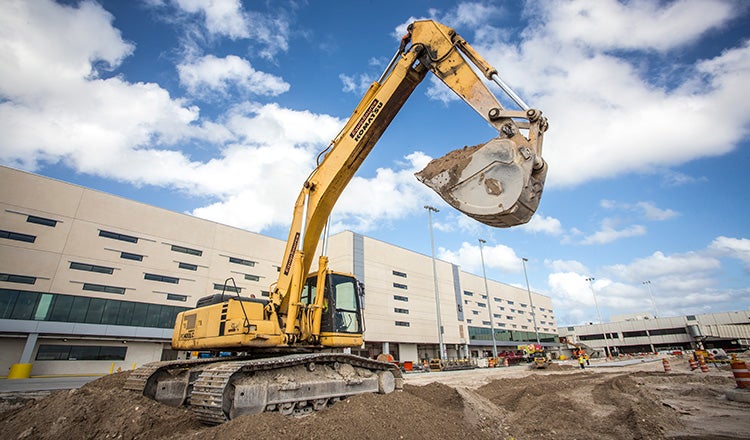
Understand Your Role & Responsibilities in CMAR to Avoid Delays
Collaboration requires the input of many parties. As in any partnership or team, it’s important that each member has a good understanding of their role, for two main reasons.
First, for those less familiar with the CMAR approach, the collaborative, iterative process can be less comfortable. A common reaction is to add multiple new layers of approval to oversee the project. This response risks bogging down a project in reviews and second guessing. Instead, empowering trusted representatives from each group — including the owner — to make key decisions can help keep projects moving and maintain schedules. This requires a strong understanding of the CMAR process to know which voices are critical to include at each stage.
Second, a good grasp of CMAR means that the team will know what items to prioritize at which stage. For example, as a designer we may advance design differently knowing that we will want the input from the contractor on specific items. Having worked on previous CMAR projects, we know that the contractor may have important considerations that would influence, for instance, the location of a retaining wall, and as a result it doesn’t make sense to advance its design too far without getting their input. This shift in perspective is what helps unlock the benefits of CMAR, but it requires a keen understanding of the delivery method.
Bonus: Consider CMAR a Stepping Stone to Other Methods
For many airports, CMAR has become a valuable project delivery method that can provide better cost certainty and expedite schedule on their projects. But other delivery methods also rely on similar collaboration between designer and contractor to lead to these benefits. As they become more comfortable with alternative delivery methods, airports may also wish to consider progressive design-build or even integrated project delivery, which also rely heavily on contractor integration in the early stages of a project.
In progressive design-build, the owner selects a design-builder based on qualifications early in the project development process and then the design-builder assists the owner with risk identification and scope, and then develops the design. As the design is developed, price, schedule and other commitments are negotiated, and when the owner and design-builder agree, a new contract is written for the construction. The percentage of design complete that this guaranteed maximum price is produced can vary but is often around 60%. Advantages of the PDB approach include a single point of responsibility, selection based on qualifications and an emphasis on innovation and collaboration between designer, contractor and owner.

Integrated project delivery is less well known, but it was added in the most recent FAA reauthorization bill as an authorized delivery method for FAA projects. Unlike traditional hierarchical contract arrangements, it relies on a “multi-party agreement” where all key parties sign onto one contract — binding them together through shared risk and responsibility. This results in all parties having a “shared risk, shared reward” contractual agreement that means that they share profits as well as losses.
Both PDB and IPD methods offer many of the same benefits as CMAR, however by selecting designer and contractor concurrently there can be even more potential for schedule improvement and allocation of risk.
An Alternative Mindset
Airports choose an alternative delivery method because it holds the promise of more positive project outcomes. But achieving those benefits isn’t as simple as changing the method on paper. Any alternative delivery project requires a related shift in mindset by project leaders and in behavior by all participants. And for CMAR, that starts with three main ideas: Engage early, prioritize collaboration and build a committed team with a deep understanding of the intricacies of the delivery method.